Rubber roofing has gained popularity due to its:
- Durability 💪
- Versatility 🎭
- Cost-effectiveness 💰
Whether you’re considering a rubber roof for your residential or commercial property, it’s essential to understand the various aspects of rubber roofing, including its pros and cons, different types, installation costs, and maintenance requirements.
We’ve put together a detailed rubber roofing cost guide that will help you understand if this is the right roofing project for you!
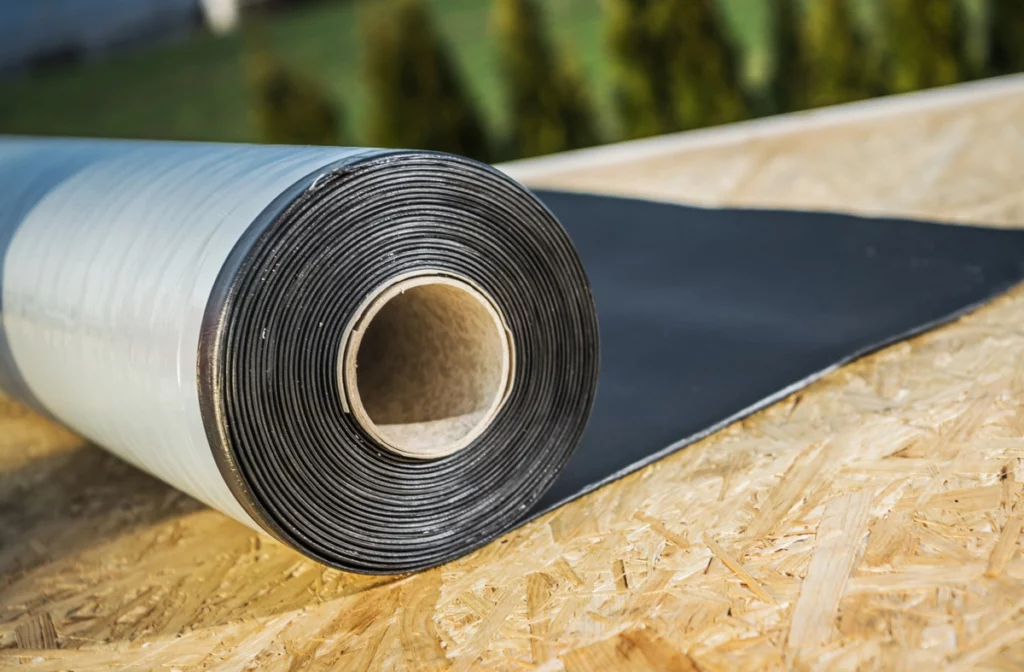
Pros and Cons of Rubber Roofs
Rubber roofs may be a popular roofing material, but understanding the pros and cons are key in order to ensure that you are choosing the right roof for your property.
👍 Pros of Rubber Roofing
- Durability: One of the most significant advantages of rubber roofing is its exceptional durability. Rubber roofs can last up to 50 years or more when properly installed and maintained. This longevity makes them a cost-effective choice over time, as they require fewer replacements compared to traditional roofing materials.
- Weather Resistance: Rubber roofing materials, such as EPDM (ethylene propylene diene terpolymer) and TPO (thermoplastic olefin), are highly resistant to harsh weather conditions, including UV rays, extreme temperatures, and heavy rain. They can withstand the elements and maintain their integrity for years.
- Energy Efficiency: Rubber roofing is known for its energy-efficient properties. Reflective rubber roofing options can help reduce heat absorption, leading to lower cooling costs during hot summer months. This energy efficiency can result in significant long-term savings on utility bills.
- Low Maintenance: Rubber roofing requires minimal maintenance compared to other roofing materials. Regular inspections and cleaning are usually sufficient to keep your rubber roof in good condition. This reduces the overall cost of ownership and maintenance over the years.
- Eco-Friendly: Rubber roofing is an eco-friendly option, as it is often made from recycled materials. Additionally, its long lifespan reduces the need for frequent replacements, which can help reduce the environmental impact associated with roofing materials.
Cons of Rubber Roofing
- Initial Cost: While rubber roofing offers long-term cost savings, the initial installation cost can be higher than some other roofing materials. However, the investment is often justified by the durability and energy efficiency benefits.
- Aesthetic Appeal: Rubber roofing may not be the most aesthetically pleasing option for some homeowners. Its appearance is quite different from traditional roofing materials like asphalt shingles or clay tiles. However, this can be mitigated by choosing a rubber roofing type that suits your preferences.
- Vulnerability to Punctures: Rubber roofs can be susceptible to punctures from sharp objects or falling branches. While they are generally resilient, it’s essential to take precautions and ensure proper maintenance to prevent damage.
- Limited Color Options: Rubber roofing typically comes in limited color options compared to other materials. This may limit your ability to match the roof with your property’s exterior aesthetics.
4 Types of Rubber Roofing
1) EPDM Roofing:
EPDM (ethylene propylene diene terpolymer) roofing is a popular choice for flat and low-slope roofs. It is a single-ply rubber membrane that offers excellent weather resistance and durability. EPDM roofing is available in rolls, making installation relatively straightforward.
2) TPO Roofing:
TPO (thermoplastic olefin) roofing is another single-ply rubber membrane option. It is known for its energy-efficient properties and white reflective surface, which helps reduce cooling costs. TPO roofing is also resistant to UV rays and chemical exposure.
3) Modified Bitumen Roofing:
Modified bitumen roofing combines asphalt with rubber or plastic modifiers to enhance its durability and weather resistance. It is commonly used on flat and low-slope roofs and comes in rolls or sheets.
4) Rubber Shingles:
Rubber shingles are designed to mimic the appearance of traditional roofing materials, such as wood or asphalt shingles. They offer the benefits of rubber roofing while providing a more traditional aesthetic. Rubber shingles are available in various colors and styles.
Rubber Roof Installation Cost
The cost of installing rubber roofing can vary significantly depending on various factors, including the type of rubber roofing, the size and complexity of your roof, and your location. On average, you can expect to pay between $6 and $12 per square foot for rubber roofing installation. Here’s a breakdown of the cost factors:
- Type of Rubber Roofing: Different types of rubber roofing materials have varying price points. EPDM and TPO are typically more affordable options, while rubber shingles and modified bitumen roofing can be on the higher end of the price spectrum.
- Roof Size and Complexity: The size and complexity of your roof will impact the installation cost. Larger roofs will naturally require more material and labor, increasing the overall cost. Additionally, roofs with multiple angles and obstructions may require more time and expertise.
- Labor Costs: Labor costs can vary based on your location and the roofing contractor you hire. It’s essential to obtain quotes from multiple contractors and consider their experience and reputation in the industry.
- Additional Materials: Installation may require additional materials such as insulation, adhesives, and sealants. These materials will contribute to the overall cost of the project.
- Roof Preparation: If your existing roof needs repairs or preparation work before the rubber roofing can be installed, this will also affect the total cost.
To get an accurate estimate for your rubber roofing installation, it’s advisable to request quotes from several roofing contractors in your area. This will help you compare costs and make an informed decision.
Tips for Maintaining Your Rubber Roof
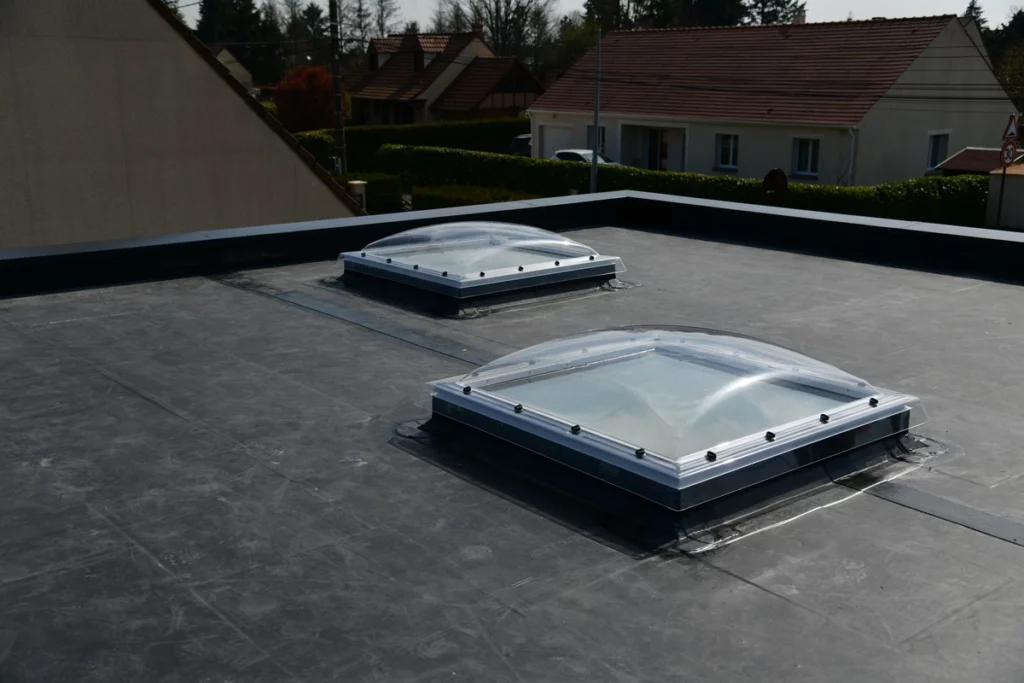
Proper maintenance is essential to maximize the lifespan of your rubber roof and avoid costly repairs. Here are some maintenance tips:
Regular Inspections 🔍
Conduct visual inspections of your rubber roof at least twice a year, ideally in the spring and fall. Look for signs of damage, punctures, or areas where the membrane may have lifted.
Clean Gutters and Drains 🍂
Keep gutters and roof drains clear of debris to ensure proper water drainage. Standing water can lead to leaks and roof damage.
Remove Snow and Debris ❄️
After heavy snowfall or storms, remove accumulated snow and debris from your roof to prevent excess weight and potential damage.
Avoid Harsh Chemicals ☠️
When cleaning your rubber roof, use gentle, non-abrasive cleaning solutions and a soft-bristle brush. Avoid harsh chemicals that can damage the rubber membrane.
Seal Seams and Flashing 👌
Inspect seams, flashing, and penetrations (vents, chimneys, etc.) for any signs of wear or damage. If necessary, reseal or repair these areas to prevent leaks.
Prevent Foot Traffic 🦶
Limit foot traffic on your rubber roof to minimize the risk of punctures or damage. If access is required, use walkway pads or boards to distribute weight evenly.
Professional Rubber Roof Installation
Rubber roofing offers an array of benefits, including durability, weather resistance, energy efficiency, and eco-friendliness. While the initial installation cost may be higher than some other roofing materials, the long-term savings and low maintenance requirements make it a cost-effective choice for many property owners. Whether you opt for EPDM, TPO, rubber shingles, or modified bitumen, proper installation and maintenance will ensure your rubber roof serves you well for decades to come, making it a worthwhile investment in the long run. Contact Johnson Restoration today in order to schedule your rubber roof installation!